Improving Energy Efficiency using Energy Recovery Wheels
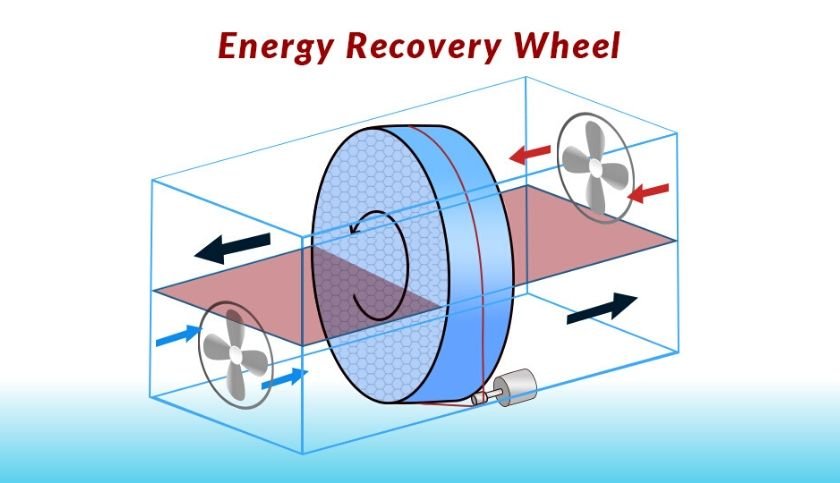
However, the difference in humidity and temperature levels can be a cause of concern. This difference can be addressed by altering the fresh air quality entering into the facility. However, it demands enormous amounts of energy.
The challenge is how to introduce outdoor air while maintaining indoor conditions and conserving energy? Hence AHU designs constitute Energy Recovery Wheels, commonly known as ERW’s that are vital to HVAC systems. Many of the energy recovery devices transfer only heat energy. However, ERW’s a form of energy recovery ventilators (ERVs) can passively transfer heat (sensible) energy and moisture (latent) energy between the exchange of airflow into and out of the facility.
Concept:
The Energy Recovery Wheel includes
- a revolving wheel that contains absorbing materials with a large internal surface area that aids in heat exchange(energy transfer)
- the spinning wheel is coated with a desiccant material to absorb moisture that aids in the latent transfer.
Energy Efficiency:
Pharma Manufacturing demands energy consumption for production. The pharma manufacturing landscape is becoming increasingly competitive, and businesses are seeking to reduce production costs without affecting the quality of the output. This reduction of the expenses can be achieved through investing in energy-efficient technologies that may offer improvement in the process, quality leading to increased output.
Energy efficiency is one of the essential ways to save on costs leading to indirect earnings. Further, energy-efficient practices lead to sustainability, thus adding a significant component to the company’s environmental strategy and reducing emissions and carbon footprint. A focus on energy efficiency will help the plant managers to reduce energy consumption even while maintaining the quality of the medicine/output. Hence the investment in energy-efficient practices is an excellent business strategy for Pharmaceutical Manufacturing Companies.
Energy Recovery Wheels use porous materials that transfer sensible (heat) and latent (moisture) energy, reducing the wastage of already conditioned air indoors. The desiccant such as Silica Gel or other molecular sieves curtails the cost of conditioning the air leading to savings of up to 50%.
However, ERW comes with certain limitations. There is a debate about the cross-contamination caused due to fresh air for Lethal products, Oncology, or Hormone products.
The Air Exchange Matrix:
 Â
Working of ERW:
The transformation of energy happens between the supply air and exhaust air. The transfer occurs from one form of energy to another, a principle of the first law of thermodynamics. We can understand the process of heat transfer of an Energy Recovery Wheel from the illustration shown below:
Energy Recovery Wheels are placed in building ventilation systems that have exhaust air and relatively high levels of outside air in different directions yet adjacent to each other. When the ERW rotates, one half of the wheel is exposed to outdoor air and the other half to the contaminated air. This process establishes a counter flow exchange where ERW absorbs the desired humidity and temperature from the outside air, and passively creates the desired temperature within the building as different mechanisms drive them.
The rotating wheel facilitates the exchange of energy from the higher airstream to the lower air stream through sensible energy, i.e., honeycomb matrix of metal and a moisture absorbing material such as silica gel. The outside and inside air is lined up in a parallel ducting. As the outdoor air passes through the ERW, one half of the wheel that is exposed absorbs the sensible and latent energy. It carries this energy inside, transferring the inside air to be released, keeping the airflows separate. The exchanged air that enters the premises is either warm or cold due to the physical properties of the Energy Recovery Wheel. ERW aids in recycling the useful features of air already inside the building rather than using new energy, meaning the exhaust air preheats the supply air in the winter. It pre-cools the supply air in the summer. The desiccant coating achieves this. Some systems use Energy Recovery Wheels to reheat supply air after it has been cooled—an effective means of humidity control.
Purge:
During the process, when the wheel rotates through the contaminated exhaust airstream to outdoor airstream, a fraction of the contaminated exhaust air gets trapped in the flutes of the wheel. This can cause leakage to the opposing supply airstream.
Any gaps during the construction of the ERW can cause air leakage from the exhaust to the supply side. If not addressed, this results in contamination of the indoor air quality.
A Purge Section added to the design can eliminate cross-contamination. The purge section employs the pressure difference between the outdoor and the return air to purge the contaminated exhaust air with clean air before it enters the supply airstream.
At the commencement of any project, Fabtech’s designing team does a recce for energy efficiency inclusive of the weather conditions in that area. It suggests appropriate outcomes to achieve greater efficiency, minimising operational costs and is environment-friendly.
Categories
Recent Posts
Subscribe
Never miss a post from Fabtech. Sign up to receive updates direct to your inbox.